Introductions
The exponential growth in the development of automation and robotics goes hand-in-hand with the increasing need for technology across various industries like automotive, packaging, and foundries. After all, opposable thumbs can only do much in manufacturing, and many processes from the mentioned industries often handle hazardous materials or their process undergoes extreme temperatures. The demand for factory-made goods is constantly rising. Finally, automating the industry sector is a much more cost-effective investment in the long run.
One of the more common, and perhaps one of the most critical components of robotic tooling, are end effectors, also known as ‘end of arm tooling’ - versatile tools that can perform specific tasks in the manufacturing process with precision.
What is an End Effector?
Automation in the manufacturing process varies according to the task, and one of the most commonly recognized is the robotic arm. But an articulated robotic arm must have an attached tool at its end. These are called end effectors - any peripheral device or tool attached to the end of a robotic arm, which serves as its 'hand.' It comes in many designs and can accomplish a wide range of tasks that requires precision and repeatability.
Common end effectors applications often mimic human hands for picking up and assembling components to manufacture a product. Others are attached tools for drilling, cutting, and other manufacturing processes.
3 Basic Types of End Effectors
End effector designs vary but are usually classified according to their fundamental purposes.
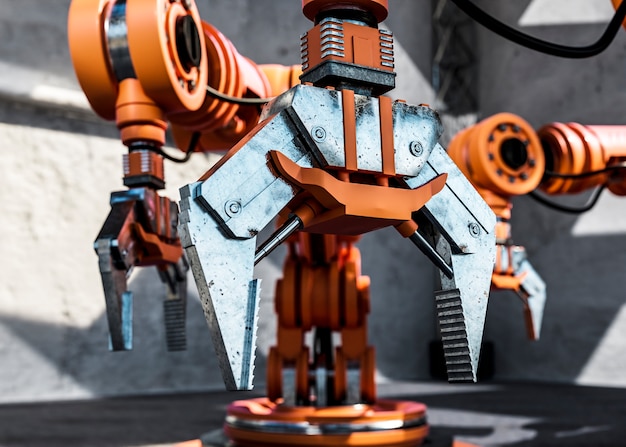
Grippers
Grippers are commonly used robot end effectors designed to grasp and manipulate objects during manufacturing. A gripper's primary function is to hold, pick, move, or perform specific actions on objects.
Grippers are well-suited tools for tasks that need to be efficient, cost-effective, and safe for workers, as some material-handling processes may have issues when done through manual labor, specifically on consistency, safety, and precision.
Here are some common uses of gripper end effectors:
1. Material Handling
2. Assembly Operations
3. Packaging
4. Pick and Place
5. Warehousing and Logistics
Some common types of grippers include mechanical grippers (with fingers or claws), vacuum grippers (using suction cups), magnetic grippers, and soft grippers (with compliant materials). The choice of gripper depends on factors such as the size, weight, and shape of the objects being handled, the required precision, and the environmental conditions in which the robot operates.
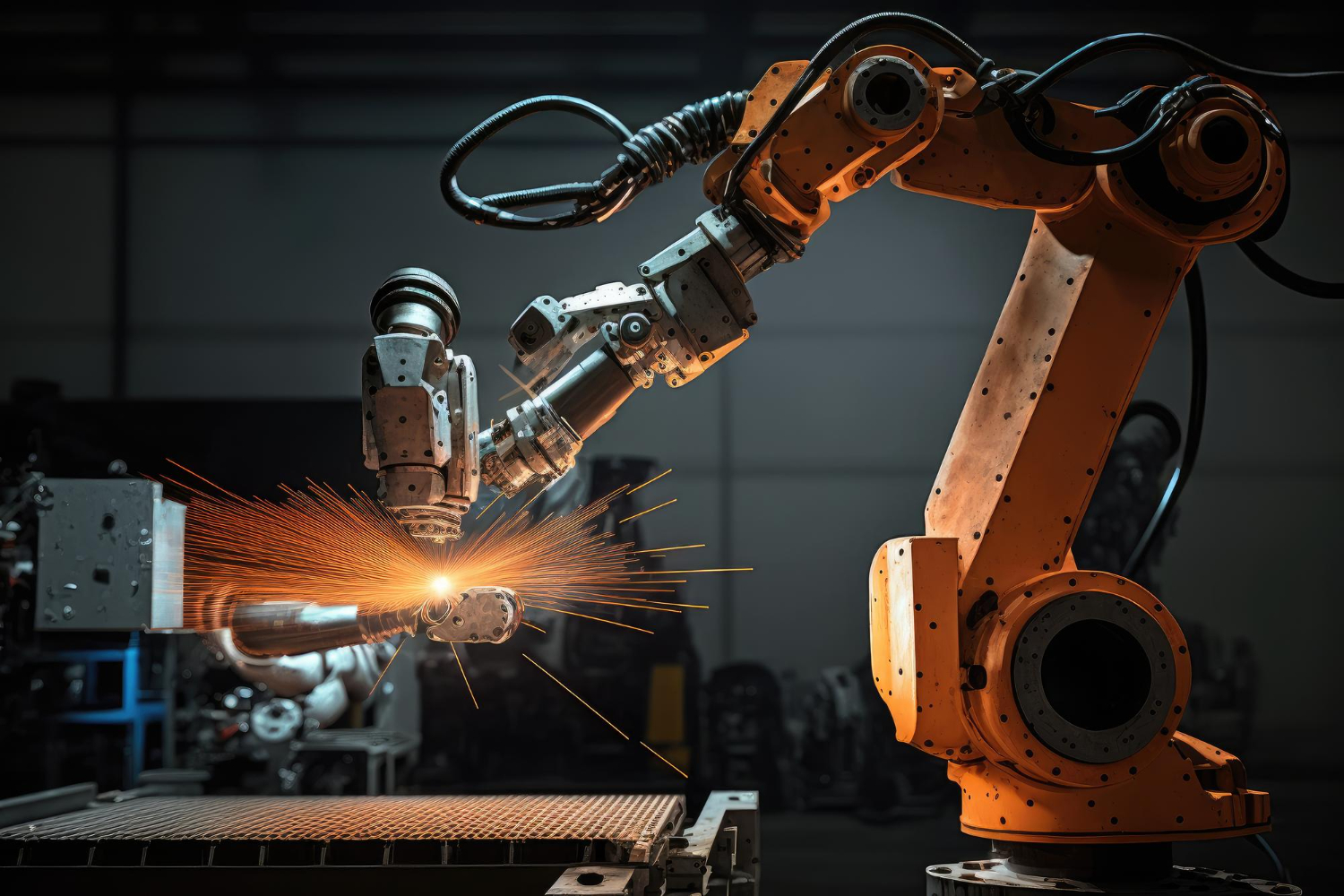
Process Tools
These end effectors are designed to process manufacturing materials. Their purpose varies more widely than grippers, and some of them are as follows:
1. Welding Guns: Robot welding tools are end effectors used for automated welding processes, such as spot welding, arc welding, and resistance welding. These tools enable robots to perform precise and repeatable welds in manufacturing applications.
2. Spray Painting Nozzles: This robot end effector is equipped with spray nozzles and used for automated painting or coating tasks. Robot painting tools ensure uniform paint application or other coatings on various surfaces.
3. Screw Tightening Tools: Robotic screw tightening end effectors are designed to drive screws into components during assembly processes accurately. They can be equipped with torque sensors to apply the desired force.
4. Dispensing Tools: These robot end effectors are used for automated dispensing adhesives, sealants, lubricants, or other liquids or materials in controlled amounts during manufacturing processes.
5. Laser Cutting Heads: End effectors equipped with laser cutting heads allow robots to perform precise cutting operations, such as laser cutting of sheet metal or other materials.
6. Grinding and Polishing Tools: robotic grinding and polishing end effectors are used to automate the grinding and polishing processes for smooth and consistent surface finishes.
Though the process is seemingly simple, like welding, and cutting objects, these end effectors are custom-designed to fit a particular purpose in the manufacturing process. While standard design specifics like safety, compliance with regulations, and cost-effectiveness are critical, the following factors decide how a process tool is designed.
1. Task Requirements: Whether it's gripping, welding, painting, cutting, or any other manufacturing process, the design must be optimized to achieve the desired functionality.
2. Payload and Weight: The end effector's design should be able to handle the weight and size of the objects or components it will be working with. While still maintaining precision and accuracy.
3. Material and Surface Characteristics: The properties of the materials being handled can significantly impact the design. Delicate or irregularly shaped objects and heavy, rigid components.will have differently designed to cater to the manufacturing material specifics.
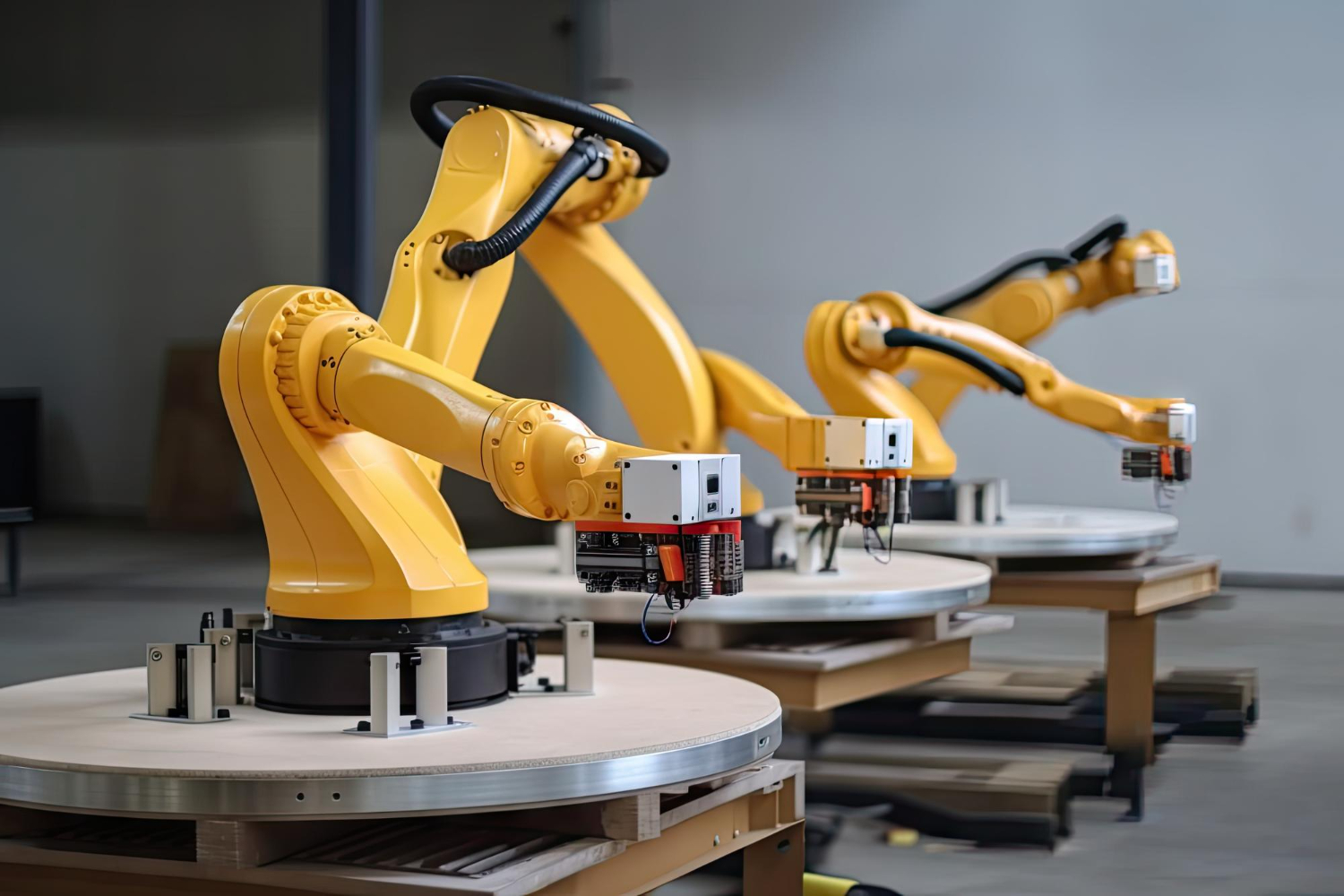
Sensors
Sensors as end effectors can be stand-alone, but they commonly serve as an auxiliary for grippers and process tools. Gripper may have them for object detection to ensure that manufacturing materials are handled according to the task required, such as correct position and orientation. Sensors are also helpful for grippers for force control to prevent damage from end effectors' grip, which is especially useful if the handled objects are delicate or irregularly shaped. Lastly, gripper sensors also help the maintenance team to handle repairs and calibrations to keep the precision and reliability of the end effectors consistent.
Sensors for process tools end effectors are much more helpful, as they fulfill the consistency of quality control of the manufacturing process, adaptability in case the materials are varied, fault detection, and preventive maintenance.
Sensor designs vary based on their purpose. The following are some of the more common sensor end effectors used:
1. Cameras
2. Proximity sensors
3. Infrared sensors
4. Light sensors
Robotic Force Compliance End Effectors: What Are They?
Handling delicate materials for manufacturing and assembly requires more precise and complex end effectors, as well as sensors to accompany process tools and grippers. Also known as force/torque sensors, robotic force compliance end effectors are typically attached at the tip of the robotic arm.
The primary purpose of force compliance in robotics is to sense the forces and torques exerted during interactions with the environment. The robot arm can adjust its movements and apply the appropriate force to perform the task safely and precisely. Alongside handling delicate objects, robotic force compliance end effectors are also helpful for smaller yet more complex assembly tasks and are able to adapt to manufacturing materials that vary in shape, weight, strength, and size.
There are two types of force-compliant end effectors:
Active Compliant Technology
Active compliant end effectors are automated systems that adjust the grip and apply forces based on real-time feedback from the integrated sensors and actuators. And as such, they are adaptive to the task required and can handle operations precisely.
They are often used for the complex and delicate manufacturing process in which there is a need for precision in industries that require assembly from small components, fragile materials, and other tasks that can be automated or at least only require minimal input from a manual robot controller. Therefore active compliant end effectors are more used in industries that make electronics, pharmaceutical companies, and the automotive industry, specifically from their complex processes and delicate components and materials.
Having a complex and precise design and made with the right robot programming software, active compliant end effectors are expectedly more expensive for purchase and maintenance.
Passive Technology
Passive-compliant end effectors do not have any built-in actuators or sensors. Instead, they are static tools or grippers that rely on the robot's motion and control to perform tasks. A passive end effector is simple and often designed for specific applications.
These devices could exist with sensors like simpler collision detectors, force sensors, or torque limitation devices to control the amount of gripping force. They are often used for manufacturing processes in which materials are flat or strong enough to be handled by a gripper. Moreover, passive-compliant end effectors are usually intended for processes when human input is required to operate the devices to make manual adjustments during the operations.
They are often lightweight in terms of components and are less expensive but lack the adaptability of active-compliant technology.
Whether an operation requires passive or active compliant end effectors depends primarily on the necessary task. Moreover, it is expected that the whole operation uses the combination of both robotic force compliance end effectors across the entire manufacturing process.
How Much Does an End Effector Cost?
Our discussion with active and passive compliant end effectors touches on how much end effectors should cost. But complexity and functionality aren't just the reason. Here are some other factors that affect the price of end effectors:
1. Customization - alongside the complex components required to produce specific end effectors, customization of the types like grippers and process tools also affects the cost, as they involve additional design and development costs, as well as additional components like sensors.
2. Material and Build Quality - A custom end effector may require specific materials to build them, and higher-quality materials translate to an increase in the cost of the devices.
3. Technology and Innovation - R&D investment and patent-related costs may also affect the pricing.
4. Regulatory Compliance - regulated industries may have specific standards and certifications for end effectors and may add cost.
Where to Find the End Effectors That Work for You?
At DMT, we are your premier partner for robotic tooling and end effectors solutions. With our full-service design and build facility, we bring your automation needs to life through expert 2D and 3D tooling design services. Our team is adept at working with various CAD software, with Unigraphics and Catia as our primary design programs. Backed by over 30 years of experience in robotic tool design and assembly, we have a proven track record in delivering innovative solutions for automotive plants' stamping, body shop, assembly, and injection mold areas.
As a testament to our commitment to excellence and efficiency, we boast an in-house CNC machine shop that enables us to manufacture our products rapidly without compromising quality. This advantage allows us to ensure fast deliveries and maintain complete control over the manufacturing process, resulting in top-notch products that cater precisely to your requirements.
Let us know how DMT can unlock the true potential of automation for your business with cutting-edge robotics expertise, seamless design and build capabilities, and rapid product delivery – all backed by decades of industry experience.